Tema proiectului
Studiu tehnico economic privind constructia produsului P,
procesul tehnologic de fabricare a reperului R si proiectarea echipamentului
tehnologic E,
P:
instalatie ungere
.
R:
reductie
E:
..
1.
Date initiale generale
Programa
de productie: 5000 buc/an
Unitatea
de productie: S.C. Faur S.A.
Obiectiv
principal: introducerea unei noi tehnologii
Fond
real de timp: 255x1x8 = 2040 ore/an
Cerinta
economica: cost minim de fabricatie.
2.
Analiza constructiva functional
tehnologica
2.1.
Schite
constructive ale produsului si reperului
Schita
reperului Reductie se prezinta in fig 2.2, unde Sk , k = 1, 2,
. sunt suprafete definitorii
2.2.
Caracteristici constructive
prescrise reperului
a.
Caracteristicile suprafetelor
Caracteristicile principale ale suprafetelor Sk
se prezinta in
tabelul 2.1
Tabelul 2.1
|
Sk
|
Forma
|
Dimensiuni
|
Rugozitate
|
Toleranta
de forma
|
Pozitia
reciproca
|
Alte conditii
(duritate, acoperiri de protectie etc.)
|
|
S1
|
plana
|
12 0+0.06x12x35
|
6,3
|
|
|
260 HB zincare
|
|
S2
|
profilata
|
Φ44/2x60˚
|
12,5
|
|
|
260 HB zincare
|
|
S3
|
elicoidala
|
M35x4,5
|
3,2
|
|
|
260 HB zincare
|
|
S4
|
cilindrica
|
Φ32x4,5
|
12,5
|
|
|
260 HB zincare
|
|
S5
|
conica
|
4,5x30˚
|
12,5
|
|
|
260 HB zincare
|
|
S6
|
plana
|
Φ32/26,8
|
12,5
|
|
|
260 HB zincare
|
|
S7
|
plana
|
Φ35/ Φ32
|
12,5
|
|
|
260 HB zincare
|
|
S8
|
cilindrica
|
Φ16x48
|
12,5
|
|
|
260 HB zincare
|
|
S9
|
plana
|
Φ76/ Φ44
|
12,5
|
|
|
260 HB zincare
|
|
S10
|
conica
|
2x45˚
|
12,5
|
|
|
260 HB zincare
|
|
S11
|
elicoidala
|
M80
|
3,2
|
|
|
260 HB zincare
|
|
S12
|
conica
|
2x45˚
|
12,5
|
|
|
260 HB zincare
|
|
S13
|
cilindrica
|
Φ60-0,06-0,02x16
|
3,2
|
|
|
260 HB zincare
|
|
S14
|
conica
|
1x45˚
|
12,5
|
|
|
260 HB zincare
|
|
S15
|
plana
|
Φ58/ Φ48
|
12,5
|
|
|
260 HB zincare
|
|
S16
|
elicoidala
|
M48x2
|
3,2
|
|
|
260 HB zincare
|
|
S17
|
profilata
|
Φ60/ Φ60x10˚
|
12,5
|
|
|
260 HB zincare
|
|
S18
|
plana
|
Φ76/ Φ56
|
12,5
|
|
|
260 HB zincare
|
|
S19
|
plana
|
21x26,6
|
12,5
|
|
|
260 HB zincare
|
|
S20
|
plana
|
21x26,6
|
12,5
|
|
|
260 HB zincare
|
|
S21
|
cilindrica
|
Φ65x4
|
12,5
|
|
|
260 HB zincare
|
|
S22
|
profilata
|
Φ56/ Φ65x60˚
|
12,5
|
|
|
260 HB zincare
|
Simbol
|
Descriere
|
0,5
.3
|
3
..6
|
6
..30
|
30
.120
|
m
|
mijlocie
|
±0,1
|
±0,1
|
±0,2
|
±0,3
|
|
|
|
|
|
|
|
|
|
|
|
|
|
b.
Caracteristici de material
prescrise
Piesa analizata este confectionata dintr-un otel
aliat constructiei de masini STAS 791 88 marca 40Cr10.
In tabelul 9.17[6] este prezentata compozitia chimica a
materialului.
Marca
otelului
|
Calitatea
|
Compozitia
chimica %
|
C
|
Mn
|
S
|
P
|
Cr
|
Ni
|
Mo
|
Alte
elemente
|
40Cr10
|
|
0,35
0,42
|
0,30
0,60
|
max
0,035
|
max
0,025
|
1,35..1,65
|
|
0,150,25
|
Si=0,20..0,45
Al=0,70..1,10
|
S
|
0,020..0,040
|
X
|
max
0,025
|
XS
|
0,020..0,035
|
In tabelul 9.18[6] sunt prezentate caracteristicile mecanice
Marca
otelului
|
Diametrul
probei de tratament termic de referinta
|
Felul
tratamen-tului termic
|
Caracteristici
mecanice
|
Limita
de curgere Rpo,z [N/mm2min]
|
Rezistenta
la rupere Rm, N/ mm2
|
Alungirea
la rupere A5%, min
|
Gatuirea
la rupere Z, %min
|
Rezilienta
KCU 300/2 J/cm2min
|
Energia
de rupere J,min
|
Duritatea
Brinell in stare necoapta HB max
|
40Cr10
|
30
|
CR
|
830
|
min
980
|
14
|
50
|
88
|
|
229
|
CR calire revenire inalta
In tabelul 9.20 sunt prezentate tratamentele termice aplicate
materialului.
Marca
otelului
|
Recoacere
de inmuiere
|
Normalizare
|
Cementare
|
Calire
I
|
Recoacere
intermediara
|
Calire
II
|
Revenire
|
Temperatura °C
|
Mediul de racire
|
Temperatura °C
|
Mediul de racire
|
Temperatura °C
|
Mediul de racire
|
Temperatura °C
|
Mediul de racire
|
Temperatura °C
|
Mediul de racire
|
Temperatura °C
|
Mediul de racire
|
Temperatura °C
|
Mediul de racire
|
40Cr10
|
710..
740
|
C
|
930..960
|
aer
|
|
|
925..955
|
u
|
|
|
|
|
590..690
|
a;u
|
c.
Masa reperului
Acasta se identifica din desenul de executie al piesei.
Astfel : m = 0,900 kg
d. Clasa de piese
Avand in vedere forma de gabarit, forma si pozitia
suprafetelor componente, se apreciaza ca reperul face parte din
clasa Arbori.
2.3.
Tehnologicitatea constructiei reperului
a. Gradul de unificare a
elementelor constructive (λe)
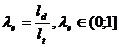
unde:
este numarul
dimensiunilor diferite, iar
numarul total al
elementelor.
Se analizeaza urmatoarele grupe principale de caracteristici
geometrice, dupa cum urmeaza
suprafete filetate 
canale
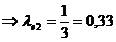
tesituri

Gradul mediu de unificare constructiva
este
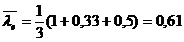
b. Concordanta dintre
caracteristicile constructive prescrise si cele impuse de rolul
functional/tehnologic
Gradul de concordanta dintre caracteristicile constructive
(CC) prescrise si cele impuse de rolul functional/tehnologic,
este:

unde: Cc este numarul CC prescrise care sunt in
concordanta cu cele impuse de cerintele functional tehnologice, iar ct
numarul total al CC prescrise.
Analiza caracteristicilor prescrise produsului si reperului
considerat prin proiectul initial a reliefat ca j caracteristici prescrise
reperului nu sunt in concordanta cu cele impuse de cerintele
functional tehnologice. Astfel, initial,
este
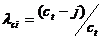
S-au propus urmatoarele modificari:
prescrierea
tolerantei 0,06 pentru suprafata S1
prescrierea
tolerantei 0,04 pentru suprafata S13
prescrierea
rugozitatii 3,2 pentru suprafatele filetate
prescrierea
rugozitatii 3,2 pentru suprafata S13
prescrierea
rugozitatii 6,3 pentru suprafaia S1
Dupa operarea modificarilor propuse:
= 1 .
c. Conditii de
tehnologicitate impuse de unificarea constructiva
Din punct de vedere al conditiei principale impuse de unificarea constructiva,
respectiv numar minim posibil al dimensiunilor elementelor constructive
(v,
), se apreciaza ca aceasta este acceptabila.
d. Conditii de
tehnologicitate impuse de procedeele tehnologice
Conditiile de tehnologicitate impuse de procedeele tehnologice de
fabricare sunt prezentate in tabelul 2.6.
Nr. crt.
|
Conditie
|
Grad de satisfacere
(da sau nu)
|
1
|
Forma de gabarit
sa prezinte axe sau plane de simetrie care dupa caz sa fie
utilizate pentru definirea planului (planelor) de separatie asociate
semimatritelor
|
DA
|
2
|
Anumite elemente
constructive (imbinari, racordari, grosimi de pereti) de
dimensiuni l sa indeplineasca conditia l≥lmin
sau/si l≤lmax, unde lmin, lmax
valori limita impuse de procedeul tehnologic
|
DA
|
3
|
Forma sau
pozitia unor suprafete sa fie astfel incat sa prezinte
inclinari in raport cu planul (planurile) de separatie a semimatritelor
pentru a permite indepartarea usoara a semifabricatului din
semimatrite
|
DA
|
4
|
Alezajele
sa fie patrunse pentru a permite rezemarea miezurilor la ambele
extremitati
|
DA
|
5
|
Elementele
constructive de rezistenta sa fie pline (sau tubulare) pentru
a evita utilizarea de miezuri
|
DA
|
6
|
Suprafetele
de intindere mare sa fie intrerupte prin canale sau denivelari
|
DA
|
7
|
Trecerile dintre
anumite suprafete cilindrica plana de precizie ridicata
sa fie sau nu sub forma de degajare (canale) in functie de cerintele
functionale si/sau de cerinta impusa de procedeul
tehnologic de prelucrare
|
DA
|
8
|
Forma si
pozitia bisajelor, gaurilor sau locasurilor sa fie astfel
incat sa conduca la un numar minim de pozitii ale piesei
sau sculei in timpul operatiei, la acces usor al sculelor in zona
de prelucrare etc.
|
DA
|
9
|
Forma si
pozitiile suprafetelor sa fie astfel incat sa
permita prinderi simple si sigure in timpul operatiilor
|
DA
|
3.
Semifabricare si
prelucrari
3.1.
Semifabricare
Se cunosc:
materialul
prescris 40Cr10, forma si dimensiunile prescrise, programa de
productie data: 5000 buc/an.
caracteristicile
semifabricatelor, metodelor si procedeelor de semifabricare
Avand in vedere considerentele de mai sus, se adopta
doua variante tehnic acceptabile de semifabricare prezentate in tabelul
3.1.
Var.
|
Semifabricat
|
Metoda de
semifabricare
|
Procedeul de
semifabricare
|
I
|
Semifabricat cu
adaosuri de prelucrare relativ mici ↔ SF1 fig. 3.1.
|
deformare la
cald
|
matritare
pe masini de forjat verticale
|
II
|
Semifabricat cu
adaosuri de prelucrare relativ mari ↔ SF2 fig. 3.2.
|
laminare
|
debitare din
bara laminata
|
Desenele semifabricatelor SF1 si SF2 se prezinta pe paginile
urmatoare.
3.2.
Prelucrari
Se cunosc:
caracteristicile
geometrice forma, dimensiunile, pozitia prescrise suprafetelor
(vezi desen reper), materialul prescris 40Cr10, programa deproductie 5000
buc/an
caracteristicile
diferitelor procedee de prelucrare prin deformare plastica la rece,
aschiere, electroeroziune etc.
Avand in vedere considerentele de mai sus, pentru fiecare
suprafata sau grup de suprafete similare, s-au stabilit cite 2
variante tehnic acceptabile privind succesiunea de prelucrari necesare
(daca nu este posibil, o varianta), care se prezinta in tabelul 3.4.
Sk
|
Var.
|
Prelucrari
|
S1
|
I
|
Frezare
|
S2
|
I
|
Strunjire
degrosare
|
S3, S11,
S16
|
I
|
Strunjire
degrosare
|
Strunjire
semifinisare
|
Filetare
|
S4
|
I
|
Strunjire
degrosare
|
S5
|
I
|
Strunjire
degrosare
|
S6
|
I
|
Strunjire
degrosare
|
S7
|
I
|
Strunjire
degrosare
|
S8
|
I
|
Gaurire
|
S9, S18
|
I
|
Strunjire
degrosare
|
S10,S12,S14
|
I
|
Strunjire
degrosare
|
S13
|
I
|
Strunjire
degrosare
|
Strunjire
semifinisare
|
Strunjire
finisare
|
S15
|
I
|
Strunjire
degrosare
|
S17
|
I
|
Strunjire
degrosare
|
S19,S20
|
I
|
Frezare
|
S21
|
I
|
Strunjire
degrosare
|
S22
|
I
|
Strunjire
degrosare
|
S23
|
I
|
Strunjire
degrosare
|
S24
|
I
|
Strunjire
degrosare
|
II
|
Adaugare
conica
|
S25
|
I
|
Strunjire
degrosare
|
II
|
Adancire
|
|
|
|
|
|
|
|
4.
Structura procesului tehnologic
de fabricare
4.1.
Structura preliminara
Se cunosc:
caracteristicile
semifabricatelor SF1 si SF2
prelucrarile
necesare
caracteristici
ale suprafetelor (vezi desen reper) si programa de productie
principiile
si restrictiile privind determinarea structurii proceselor
tehnologice
elementele
definitorii ale structurii preliminare
Avand in vedere considerentelede mai sus, s-a efectuat gruparea
prelucrarilor necesare si a altor activitatilor tehnologice
complementare necesare, in operatii principale si, respectiv,
operatii complementare, in doua variante, s-au determinat celelalte
elemente de definire a structurii preliminare a procesului tehnologic de
fabricare si, corespunzator, se prezinta mai joi cele 2 variante de
proces tehnologic de fabricare in structura preliminara PT1 si
PT2.
4.2.
Structura detaliata
Structura detaliata a fiecarei variante de proces/sistem
tehnologic s-a determinat prin dezvoltarea elementelor structurale preliminare
si prin includerea celorlalte elemente definitorii, dupa cum
urmeaza.
4.2.1.
Nomenclatorul, fazele si schemele de orientare
fixare asociate operatiilor
a.
Nomenclatorul operatiilor.
La fiecare varianta de proces tehnologic, PT1, PT2, s-au stabilit
operatiile complementare si, corespunzator, nomenclatorul
operatiilor, care se prezinta in tabelul 4.2.1.
Tabelul 4.2.1.
PT1
|
PT2
|
00.
Matritare
10. Strunjire I
15. Control
20. Strunjire II
25. Control
30. Frezare I
40. Frezare II
50. Tratament termic
60. Zincare
70. Spalare
80. Control final
90. Conservare - depozitare
|
10. Debitare
20. Strunjire I (degrosare)
30. Strunjire II (degrosare)
35. Control
40. Strunjire III (finisare)
50. Strunjire IV (finisare)
55. Control
60. Frezare I
70. Frezare II
80. Tratament termic
90. Zincare
100.
Spalare
110. Control
final
120. Conservare
- depozitare
|
b.
Fazele
si schemele de orientare fixare.
La fiecare varianta de proces tehnologic PT1, PT2, prin aplicarea
metodologiilor specific, s-au determinat fazele si schemele de orientare
fixare (SOF), fiecare dintre acestea intr-o singura varianta cu
exceptia determinarii schemei de orientare fixare optime la
operatia PT , dupa cum urmeaza:
PT1 Tabelul 4.2.2.
Operatia
|
Fazele
operatiei
|
Schita
operatiei (SOF)
|
Utilaj si
S.D.V.-uri (tip)
|
00.
Matritare
|
|
|
U:
masina de forjat
D-S:
semimatritare
V: subler
|
10. Strunjire I
|
a. Prindere semifabricat
10.1. Strunjire
degrosare contur exterior cu respectarea cotelor

10.2. Strunjire
degrosare exterioara 
10.3. Strunjire
cilindrica exterioara de semifinisare la 
10.4. Strunjire
cilindrica exterioara de finisare la 
10.5. Strunjire
contur interior cu respectarea cotelor 
10.6. Strunjire
cilindrica interioara de semifinisare la 
10.7.
Gaurire 
10.8. Filetare
interioara M48x2
b. Desprindere
si depunere piesa
|
Fig. 1
|
U: strung CNC
S: cutit,
burghiu
D: universal
V: subler,
calibru filetat
|
15. Control
|
|
|
|
20. Strunjire II
|
a. Prindere
semifabricat
20.1. Strunjire
degrosare contur exterior cu respectarea cotelor 

20.2. Strunjire
cilindrica exterioara de semifinisare la 
20.3. Strunjire
cilindrica exterioara de semifinisare la 
20.4. Strunjire
conica interioara de degrosare la 
20.5. Filetare
exterioara M35x1,5
20.6. Filetare
exterioara M80
b. Desprindere
si depunere piesa
|
Fig. 2
|
U: strung CNC
S: cutit
D: universal
V: subler,
calibru filetat
|
25. Control
|
|
|
|
30. Frezare I
|
a. Prindere
semifabricat
30.1.Frezare
canal 
b. Indexare
dispozitiv
30.2. Frezare
canal 
c. Indexare
dispozitiv
30.3. Frezare
canal 
d. Desprindere
si depunere piesa
|
Fig. 3
|
U:
masina de frezat
S: freza
D: special
V: subler,
calibru
FU1 / P20
|
40. Frezare II
|
a. Prindere
semifabricat
40.1. Frezare
laturi S = 55
b. Desprindere
si depunere piesa
|
Fig. 4
|
U:
masina de frezat
S: freza
D: special
V: subler
|
50. Tratament
termic
|
|
|
|
60. Zincare
|
|
|
|
70. Spalare
|
|
|
|
80. Control final
|
|
|
|
90. Conservare - depozitare
|
|
|
|
PT2 Tabelul 4.2.3.
Operatia
|
Fazele
operatiei
|
Schita
operatiei (SOF)
|
Utilaj si
S.D.V.-uri (tip)
|
10. Debitare
|
a. Prindere
semifabricat
10.1. Debitare
la 
b. Desprindere
si depunere piesa
|
Fig. 5
|
U:
masina de debitat
S: panglica
ferastrau
D: menghina
V: subler
|
20. Strunjire I
(degrisare)
|
a. Prindere
semifabricat
20.1. Strunjire
frontala de degrosare la 
20.2. Strunjire
cilindrica exterioara de degrosare la 
20.3. Strunjire
cilindrica exterioara de degrosare la 
20.4. Strunjire
frontala de degrosare la 4,8
20.5. Strunjire
degajare frontala 
20.6.
Tesire exterioara 
20.7.
Gaurire 
20.8. Strunjire
conica interioara de degrosare la 
b. Desprindere
si depunere piesa
|
Fig. 6
|
U: strung
frontal
S: cutit,
burghiu
D: universal
V: subler
|
30. Strunjire II
(degrosare)
|
a. Prindere
semifabricat
30.1. Strunjire
frontala de degrosare la 103,5
30.2. Strunjire
cilindrica de exterioara de degrosare la 
30.3. Strunjire
exterioara de degrosare la 
30.4. Strunjire
frontala de degrosare la 8
30.5. Strunjire
cilindrica exterioara de degrosare la 
30.6. Strunjire
degajare exterioara 
30.7. Strunjire
degajare exterioara 
30.8. Tesire
exterioara (la )
30.9.
Tesire exterioara (la )
30.10.
Largire 
30.11. Strunjire
cilindrica interioara de degrosare la 
30.12. Strunjire
frontala de degrosare la 51
30.13.
Tesire interioara 
b. Desprindere
si depunere piesa
|
Fig. 7
|
U: strung
frontal
S: cutit,
burghiu
D: universal
V: subler
|
35. Control
|
|
|
|
40. Strunjire
III (finisare)
|
a. Prindere
semifabricat
40.1. Strunjire
cilindrica exterioara de semifinisare la 
40.2. Strunjire
cilindrica exterioara de finisare la 
40.3. Strunjire
cilindrica exterioara de semifinisare la 
40.4. Filetare
interioara M48x2
40.5. Strunjire
cilindrica exterioara de semifinisare la 
40.6. Filetare
interioara M48x2
b. Desprindere
si depunere piesa
|
Fig. 8
|
U: strung
frontal
S: cutit
D: universal
V: subler,
caibru filetat
|
50. Strunjire IV
(finisare)
|
a. Prindere
semifabricat
50.1. Strunjire
cilindrica exterioara de semifinisare la 
50.2. Filetare
exterioara M35x1,5
b. Desprindere
si depunere piesa
|
Fig. 9
|
U: strung
frontal
S: cutit
D: universal
V: subler,
calibru filetat
|
55. Control
|
|
|
|
60. Frezare
|
a. Prindere
semifabricat
60.1. Frezare
canal 
b. Indexare
dispozitiv
60.2.
c. Indexare
dispozitiv
60.3.
d. Desprindere
si depunere piesa
|
Fig. 10
|
|
70. Frezare II
|
a. Prindere
semifabricat
70.1. Frezare
laturi S = 55
b. Desprindere
si depunere piesa
|
Fig. 11
|
|
80. Tratament
termic
|
|
|
|
90. Zincare
|
|
|
|
100.
Spalare
|
|
|
|
110. Control
final
|
|
|
|
120. Conservare
- depozitare
|
|
|
|
c.
Determinarea SOF O pentru operatia 40. Frezare II
PT1 si operatia 70. Frezare II PT2.
Date initiale : schita simplificata a operatiei
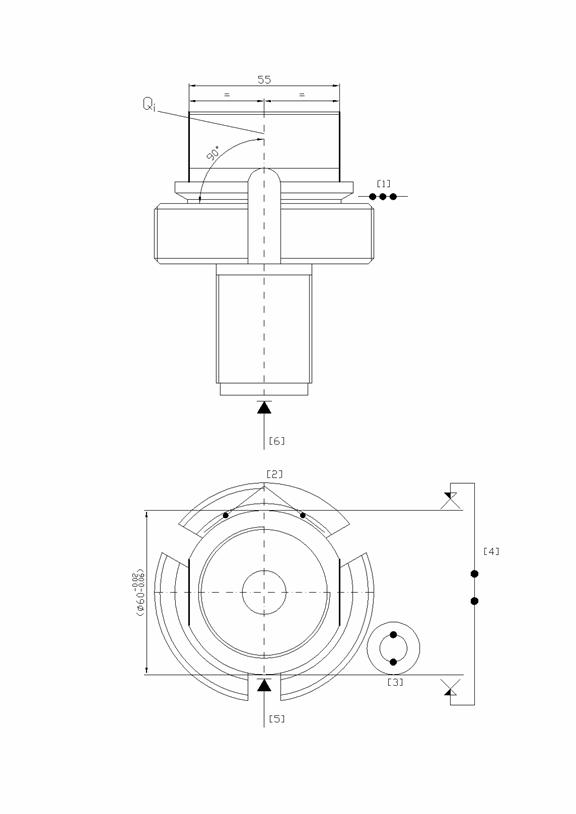
E1. Identificarea
CTO si calculul
CTO:



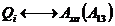
Rezulta:


BC = A18 ; 

Se adopta 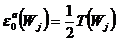
Dar
0,12 mm (ISO 2768 mk)
Astfel:
0,06 mm.
E2. EGT si E/M-O/F/R/A
EGT se stabilesc
astfel incat BT = BC , respectiv, EGT = A18, A13.
E/M-O = corespund
simbolurilor (1),[2],(3),[4].
EF : corespund
simbolurilor (5),[4],[6].
E/M-R/A: nu este
cazul.
E3 dimensiuni
definitorii ale EO, SOF-TP,
; SOF-TA; SOF-0 .
Dimensiuni
definitorii : D2 =
.
SOF-TP,
, SOF-TA : vezi tabelul 4.2.4. si 4.2.5.
tabelul 4.2.4.
E/M-0
|
[2]
|
[3]
|
[4]
|
   ( )
|
Expresie
|
jmax
|
0
|
0
|
Valoare
|
0,06
|
0
|
0
|
tabelul 4.2.5
E/M-O/F
|
SOF-TP
|

|
   ( )
|
SOF-TA
|
[1]
|
[2]
|
[3]
|
[4]
|
[5]
|
[6]
|
X
|
x
|
|
|
x
|
|
1
|
0
|
0,06
|
X
|
X
|
|
x
|
|
|
x
|
2
|
0
|
0
|
X
|
x
|
|
|
x
|
|
|
3
|
0
|
0
|
X
|
Concluzie : toate
cele 3 SOF-TP sunt SOF-TA.
SOF-0
Aceasta se
stabileste pe baza criteriului economic.
Astfel, avand in
vedere structurile celor 3 SOF-TA si costurile de executie ale
E/M-O/F
SOF-0 : .
4.2.2.
Utilajul si S.D.V.-urile, metodele si procedeele
de reglare la dimensiune
a. Utilajele (U)
Avand in vedere tipurile de utilaje adoptate, continutul
operatiilor, precum si dimensiunile de gabarit ale
semifabricatului/piesei, pentru fiecare operatie sau grup de operatii
se stabilesc utilajele, U, intr+o varianta, dupa cum se prezinta
in tabelul 4.2.2.1.
Tabelul 4.2.2.1.
PT
|
Operatia(iile)
|
U
|
Tip
|
Marca
|
Turatii(n
),
vansuri(s
)/viteze de avans(w
), putere(N), curse, etc.
|
PT1
|
10. Strunjire I
20. Strunjire II
|
Strung
CNC
|
MT32
CNC
|
Diametrul
de rotire deasupra batiului : 320 mm
Diametrul
de rotire deasupra saniei transversale : 150 mm
Alezajul
din arborele principal : 50 mm
n
(rot/min J = 0
.5000 (reglare continua))
N =
7 kw
|
30. Frezare I
40. Frezare II
|
Masina de frezat
|
FU1
1250x325
|
Dimensiunile
mesei : 1250x320 mm
n
(rot/min) : 30; 37,5; 47,5; 60; 75; 95; 118; 150; 190; 235; 300; 375; 475;
600; 750; 950; 1180; 1500.
Vslmm/min)
: 19; 23,5; 30; 28; 37,5; 60; 75; 95; 118; 150; 190; 235; 300; 375; 475; 600;
750; 950.
Vst(mm/min)
: 19; 23,5; 30; 28; 37,5; 60; 75; 95; 118; 150; 190; 235; 300; 375; 475; 600;
750; 950.
Vsv
= 0,6*Vsl
N =
7,5 kw
|
PT2
|
10. Debitare
|
Masina
de debitat cu panglica fierastrau
|
ARG 400 PLUS
|
VS
= 16
.80 mm/min
V =
37
..95 m/min
N :
11 kw
|
20. Strunjire I
30. Strunjire II
40. Strunjire
III
50. Strunjire IV
|
Strung frontal
|
SN 250
|
n[rot/min]
: 63; 90; 125; 180; 250; 355; 500; 710; 1000; 1410; 1910; 2800.
Sl
(mm/rot) : 0,04; 0,05; 0,06; 0,07; 0,08; 0,10; 0,12; 0,14; 0,16; 0,20; 0,24;
0,28; 0,32; 0,40; 0,46; 0,56; 0,64; 0,80; 0,96; 1,12; 1,28; 1,60; 1,92; 2,24.
St
(mm/rot) : 0,012; 0,015; 0,018; 0,021; 0,021; 0,024; 0,030; 0,036; 0,042;
0,048; 0,060; 0,072; 0,084; 0,096; 0,12; 0,144; 0,168; 0,192; 0,24; 0,288;
0,336; 0,384; 0,48; 0,516; 0,672.
N =
4,5 kw
|
60. Frezare I
70. Frezare II
|
Masina
de frezat
|
FU1 1250x325
|
Dimensiunile
mesei : 1250x320 mm
n
(rot/min) : 30; 37,5; 47,5; 60; 75; 95; 118; 150; 190; 235; 300; 375; 475;
600; 750; 950; 1180; 1500.
Vslmm/min)
: 19; 23,5; 30; 28; 37,5; 60; 75; 95; 118; 150; 190; 235; 300; 375; 475; 600;
750; 950.
Vst(mm/min)
: 19; 23,5; 30; 28; 37,5; 60; 75; 95; 118; 150; 190; 235; 300; 375; 475; 600;
750; 950.
Vsv
= 0,6*Vsl
N =
7,5 kw
|
b. Dispozitivele port piesa
(DPP)
Avand in vedere schemele de orientare fixare si
caracteristicile specifice ale utilajelor, se stabilesc dispozitivele de
prindere a piesei DPP, pentru fiecare operatie sau grup de operatii
dupa cum se prezinta in tabelul 4.2.2.2.
Tabelul 4.2.2.2.
PT
|
Operatia(iile)
|
DPP
|
PT1
|
10. Strunjire I
20. Strunjire II
|
Universal
hidraulic
|
30. Frezare I
|
Dispozitiv
special DPP-F01.00.
|
40. Frezare II
|
Dispozitiv
special DPP-F02.00.
|
PT2
|
10. Debitare
|
Menghina cu
bacuri prismatice si actionare hidraulica
|
20. Strunjire I
30. Strunjire II
40. Strunjire
III
50. Strunjire IV
|
Universal 3/160
II STAS 1655/2-87
|
60. Frezare I
|
Dispozitiv
special DPP-F01.00.
|
70. Frezare II
|
Dispozitiv
special DPP-F02.00.
|
c. Sculele de prelucrare (S)
si dispozitivele port scule (DPSc)
Avand in vedere tipurile de scle adoptate, continutul fazelor de
prelucrare, caracteristicile specifice ale semifabricatului/piesei, precum
si caracteristicile specifice ale utilajelor de prelucrare/dispozitivelor
port - scule, pentru fiecare faza sau grup de faze de prelucrare, se
stabilesc sculele, S, si, corespunzator, dispozitivele port scule,
DPSc, intr-o varianta, dupa cum se prezinta in tabelul 4.2.2.3.
Tabelul 4.2.2.3.
PT1
Operatia
|
Faza(ele) de
prelucrare
|
S
|
Fig.
|
Simbol
|
Tip
|
Notare
|
Alte
caracteristici
|
DPSc
|
10. Strunjire I
|
10.1. Strunjire
degrosare contur exterior cu respectarea cotelor
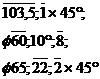
|
4.2.2.1.
|
S1
|
cutit
|
Suport PCLNR
2020 K09 / CNMG 090304 PM / P30
|
Η=5°; H1=95°
(H=95°; H1=5°)
|
Suport
port-cutit
|
10.2. Strunjire
degrosare exterioara 
|
S2
|
cutit
|
Cutit
profilat / Rp3
|
b = 4 mm
|
10.3. Strunjire
cilindrica exterioara de semifinisare la 
|
S3
|
cutit
|
Suport PCLNR
2020 K09 / CNMG 090304 PM / P20
|
H=95°; H1=5°
|
10.4. Strunjire
cilindrica exterioara de finisare la 
|
S4
|
cutit
|
Suport PCLNR
2020 K09 / CNMG 090304 PM / P10
|
10.5. Strunjire
contur interior cu respectarea cotelor 
|
S5
|
cutit
|
Suport S12M
SCLCR 06 / CNMG 060304 PM / P30
|
H=5°; H1=95°
(H=95°; H1=5°)
|
10.6. Strunjire
cilindrica interioara de semifinisare la 
|
S6
|
cutit
|
Suport S12M
SCLCR 06 / CNMG 060304 PM / P20
|
H=95°; H1=5°
|
10.7.
Gaurire 
|
S7
|
burghiu
|
Burghiu 16 STAS
575 80 / Rp 4
|
2H=118°
|
Tip
bucsa
|
10.8. Filetare
interioara M48x2
|
S8
|
cutit
|
Suport R166.4KF
16 16 / R166.OL 16MM01 200 / P20
|
ε=60°
|
Suport
port-cutit
|
20. Strunjire II
|
20.1. Strunjire
degrosare contur exterior cu respectarea cotelor 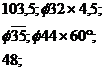 
|
4.2.2.2.
|
S1
|
|
|
|
Suport
port-cutit
|
20.2. Strunjire
cilindrica exterioara de semifinisare la 
|
S3
|
|
|
|
20.3. Strunjire
cilindrica exterioara de semifinisare la 
|
S3
|
|
|
|
20.4. Strunjire
conica interioara de degrosare la 
|
S5
|
|
|
|
20.5. Filetare
exterioara M35x1,5
|
S9
|
Cutit
|
Suport R166.4FG
1616 16 / R166.OG 16MM01 150 / P20
|
ε=60°
|
20.6. Filetare
exterioara M80
|
S10
|
Cutit
|
Suport R166.4FG
1616 16 / R166.OG 16MM01 450 / P20
|
30. Frezare I
|
30.1.Frezare
canal 
|
4.2.2.3.
|
S11
|
Freza
|
Freza
R215.44 12A16 09C / CNMG 090304 PM / P20
|
Z=1 dinte
D=12 mm
|
|
30.2.Frezare
canal 
|
30.3.Frezare
canal 
|
40. Frezare II
|
|
4.2.2.4.
|
S12
|
Tren de freze
disc
|
Freze N133.32
125S40DM 0920 / P30
|
D=100 mm
Z=8 dinti
|
Doua
port-freze
|
Tabel 4.2.2.4.
PT2
Operatia
|
Faza(ele) de
prelucrare
|
S
|
Fig.
|
Simbol
|
Tip
|
Notare
|
Alte
caracteristici
|
DPSc
|
10. Debitare
|
10.1. Debitare
la 
|
4.2.2.5.
|
S13
|
cutit
|
Panglica
fierastrau / Rp3
|
g=2 mm
|
Tip tambur
|
20. Strunjire II
|
20.1. Strunjire
frontala de degrosare la 
|
4.2.2.6.
|
S14
|
cutit
|
Suport PSSNR
2020K09 / SNMG 090304 PM / P30
|
H = H1
= 45°
|
Suport port
cutit
|
20.2. Strunjire
cilindrica exterioara de degrosare la 
|
S1
|
|
|
|
20.3. Strunjire
cilindrica exterioara de degrosare la 
|
S1
|
|
|
|
20.4. Strunjire
frontala de degrosare la 4,8
|
S1
|
|
|
|
20.5. Strunjire
degajare frontala 
|
S1
|
|
|
|
20.6.
Tesire exterioara 
|
S14
|
|
|
|
20.7.
Gaurire 
|
S7
|
|
|
|
Reductie
2/1 STAS 252-80
|
20.8. Strunjire
conica interioara de degrosare la 
|
S5
|
|
|
|
Suport port -
cutit
|
30. Strunjire II
|
30.1. Strunjire
frontala de degrosare la 103,5
|
|
|
|
|
|
|
30.2. Strunjire
cilindrica de exterioara de degrosare la 
|
|
|
|
|
|
30.3. Strunjire
exterioara de degrosare la 
|
|
|
|
|
|
30.4. Strunjire
frontala de degrosare la 8
|
|
|
|
|
|
30.5. Strunjire
cilindrica exterioara de degrosare la 
|
|
|
|
|
|
30.6. Strunjire
degajare exterioara 
|
|
|
|
|
|
30.7. Strunjire
degajare exterioara 
|
|
|
|
|
|
30.8.
Tesire exterioara (la )
|
|
|
|
|
|
30.9.
Tesire exterioara (la )
|
|
|
|
|
|
30.10.
Largire 
|
|
|
|
|
|
30.11. Strunjire
cilindrica interioara de degrosare la 
|
|
|
|
|
|
30.12. Strunjire
frontala de degrosare la 51
|
|
|
|
|
|
30.13.
Tesire interioara 
|
|
|
|
|
|
40. Strunjire
III
|
40.1. Strunjire
cilindrica exterioara de semifinisare la 
|
4.2.2.8.
|
S3
|
|
|
|
Suport port -
cutit
|
40.2. Strunjire
cilindrica exterioara de finisare la 
|
S4
|
|
|
|
40.3. Strunjire
cilindrica exterioara de semifinisare la 
|
S3
|
|
|
|
40.4. Filetare
interioara M48x2
|
S10
|
|
|
|
40.5. Strunjire
cilindrica exterioara de semifinisare la 
|
S6
|
|
|
|
40.6. Filetare
interioara M48x2
|
S8
|
|
|
|
50. Strunjire IV
|
50.1. Strunjire
cilindrica exterioara de semifinisare la 
|
4.2.2.9.
|
S3
|
|
|
|
Suport port
cutit
|
50.2. Filetare
exterioara M35x1,5
|
S9
|
|
|
|
60. Frezare
|
60.1. Frezare
canal 
|
4.2.2.3.
|
S11
|
|
|
|
|
60.2.
|
|
|
|
60.3.
|
|
|
|
70. Frezare II
|
70.1. Frezare
laturi S = 55
|
4.2.2.4
|
S12
|
|
|
|
|
d. Metodele si
procedeele de reglare la dimensiune
Avand in vedere programa de productie, continutul
operatiilor / fazelor si caracteristicile specifice ale utilajelor,
se stabilesc metodele si, respectiv, procedeele de reglare la dimensiune,
intr-o varianta, dupa cum se prezinta in tabelul 4.2.2.4.
Tabelul 4.2.2.4.
PT
|
Operatia(iile)
|
Metoda de
reglare la dimensiune
|
Procedeul(-ele)
de reglare la dimensiune
|
PT1
|
10. Strunjire I
20. Strunjire II
|
Metoda
reglarii automate (RA)
|
Reglare cu :
mecanism de orientare tip universal si reglare dupa program
|
30. Frezare I
|
Reglare cu :
elemente de orientare tip cep, inel cilindric si cu gabarit de reglare
(dupa doua directii)
|
40. Frezare II
|
|
PT2
|
10. Debitare
|
Reglare cu :
mecanisme de orientare tip menghina cu opritor mecano electric.
|
20. Strunjire I
30. Strunjire II
40. Strunjire
III
50. Strunjire IV
|
Reglare cu :
mecanism de orientare tip universal si reglare dupa gradatie
|
60. Frezare I
|
Reglare cu :
elemente de orientare tip cep, inel cilindric si cu gabarit de reglare
(dupa doua directii)
|
70. Frezare II
|
Reglare cu :
mecanism de orientare tip universal si reglare dupa gradatie
|
4.2.3.
Adaosurile de prelucrare si dimensiunile intermediare
Adaosurile de prelucrare, Ak, s-au determinat prin alegere
din tabelele normative, iar dimensiunile intermediare, L, prin calcul,
dupa cum urmeaza.
Se subliniaza urmatoarele:
; 
; 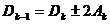
Unde: k = n, n-1,
.., 1 ; + pentru dimensiuni tip arbore, iar
pentru dimensiuni tip alezaj.
Tabelul 4.2.3.1.
Sk
|
Dimens.
Prescrisa Ln, mm
|
Adaosul total A0,
mm
|
Faza de
prelucrare
|
Nr. de ordine
si denumire preliminara
|
Ak,
mm
|
Lk,
mm
|
Nr. de ordine
si denumire finala
|
S1
|

|
12
|
30.1.Frezare
canal

|
12
|

|
30.1.Frezare
canal 
|
30.1.Frezare
canal 
|
30.1.Frezare
canal 
|
30.1.Frezare
canal 
|
30.1.Frezare
canal 
|
S2
|

|
0,9
|
20.1. Strunjire
degrosare contur exterior cu respectarea cotelor 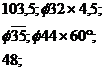

|
0,9
|

|
20.1. Strunjire
degrosare contur exterior cu respectarea cotelor
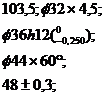

|
S3
|
M35x1,5
|
2,724
|
20.1. Strunjire
degrosare contur exterior cu respectarea cotelor 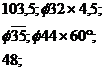

|
1,25
|
Ψ36h12
|
20.1. Strunjire
degrosare contur exterior cu respectarea cotelor
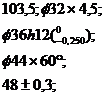

|
20.2. Strunjire
cilindrica exterioara de semifinisare la 
|
0,5(tab.
8.49(1))
|
Ψ35h10
|
20.2. Strunjire
cilindrica exterioara de semifinisare la 
|
20.5. Filetare
exterioara M35x1,5
|
0,974
|
M35x1,5
|
20.5. Filetare
exterioara M35x1,5
|
S4
|

|
1,75
|
20.1. Strunjire
degrosare contur exterior cu respectarea cotelor 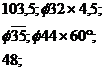 
|
1,75
|

|
20.1. Strunjire
degrosare contur exterior cu respectarea cotelor
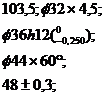

|
S5
|
4,5x30°
|
2,25
|
20.4. Strunjire
conica interioara de degrosare la 
|
2,25
|
4,5x30°
|
20.4. Strunjire
conica interioara de degrosare la 
|
S6
|
103,5
|
1,75
|
20.1. Strunjire
degrosare contur exterior cu respectarea cotelor 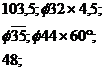 
|
1,75
|
103,5
|
20.1. Strunjire
degrosare contur exterior cu respectarea cotelor
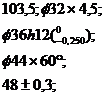

|
S7
|
4,5
|
1,75
|
20.1. Strunjire
degrosare contur exterior cu respectarea cotelor 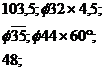 
|
1,75
|
4,5
|
20.1. Strunjire
degrosare contur exterior cu respectarea cotelor
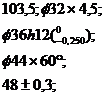

|
S8
|
Ψ16
|
8
|
10.7.
Gaurire 
|
8
|
Ψ16
|
10.7.
Gaurire 
|
S9
|
48
|
1,75
|
20.1. Strunjire
degrosare contur exterior cu respectarea cotelor 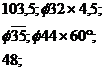 
|
1,75
|
48
|
20.1. Strunjire
degrosare contur exterior cu respectarea cotelor
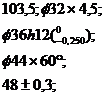

|
S10
|
2x45°
|
1,9
|
20.1. Strunjire
degrosare contur exterior cu respectarea cotelor 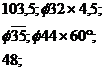 
|
1,9
|
2,7x45°
|
20.1. Strunjire
degrosare contur exterior cu respectarea cotelor
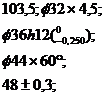

|
S11
|
M80
|
4,67
|
20.1. Strunjire
degrosare contur exterior cu respectarea cotelor 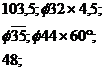 
|
1,05
|
Ψ81,4h12
|
20.1. Strunjire
degrosare contur exterior cu respectarea cotelor
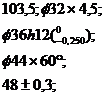

|
20.3. Strunjire
cilindrica exterioara de semifinisare la 
|
0,7 (tab.
8.49(1))
|
Ψ80h10
|
20.3. Strunjire
cilindrica exterioara de semifinisare la 
|
20.6. Filetare
exterioara M80
|
2,923
|
M80
|
20.6. Filetare
exterioara M80
|
S12
|
2x45°
|
2,6
|
10.1. Strunjire
degrosare contur exterior cu respectarea cotelor
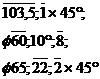
|
2,6
|
3,75x45°
|
10.1. Strunjire
degrosare contur exterior cu respectarea cotelor
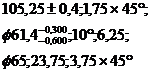
|
S13
|

|
1,75
|
10.1. Strunjire
degrosare contur exterior cu respectarea cotelor
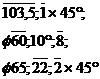
|
1,05
|

|
10.1. Strunjire
degrosare contur exterior cu respectarea cotelor
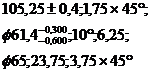
|
10.3. Strunjire
cilindrica exterioara de semifinisare la 
|
0,5(tab.
8.49(1))
|

|
10.3. Strunjire
cilindrica exterioara de semifinisare la 
|
10.4. Strunjire
cilindrica exterioara de finisare la 
|
0,2
|

|
10.4. Strunjire
cilindrica exterioara de finisare la 
|
S14
|
1x45°
|
1,2
|
10.1. Strunjire
degrosare contur exterior cu respectarea cotelor
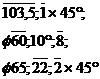
|
1,2
|
1,7x45°
|
10.1. Strunjire
degrosare contur exterior cu respectarea cotelor
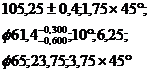
|
S15
|
103,5
|
1,75
|
10.1. Strunjire
degrosare contur exterior cu respectarea cotelor
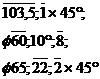
|
1,75
|

|
10.1. Strunjire
degrosare contur exterior cu respectarea cotelor
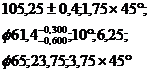
|
S16
|
M48x2
|
3,05
|
10.5. Strunjire
contur interior cu respectarea cotelor 
|
1,0
|
Ψ43,9H12
|
10.5. Strunjire
contur interior cu respectarea cotelor 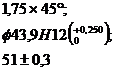
|
10.6. Strunjire
cilindrica interioara de semifinisare la 
|
0,75 (tab.
8.51(1))
|
Ψ45,4H10
|
10.6. Strunjire
cilindrica interioara de semifinisare la 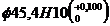
|
10.8. Filetare
interioara M48x2
|
1,299
|
M48x2
|
10.8. Filetare
interioara M48x2
|
S17
|
5x10°
|
1,2
|
10.1. Strunjire
degrosare contur exterior cu respectarea cotelor
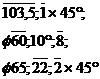
|
1,2
|
5x10°
|
10.1. Strunjire
degrosare contur exterior cu respectarea cotelor
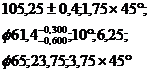
|
S18
|
22
|
1,75
|
10.1. Strunjire
degrosare contur exterior cu respectarea cotelor
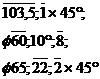
|
1,75
|
23,75
|
10.1. Strunjire
degrosare contur exterior cu respectarea cotelor
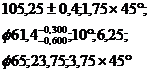
|
S19
S20
|
22
|
5
|
40.1. frezare
laturi S=55
|
5
|
55
|
40.1. frezare
laturi S=55
|
S21
|
Ψ65
|
1,75
|
10.1. Strunjire
degrosare contur exterior cu respectarea cotelor
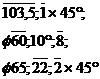
|
1,75
|
Ψ65
|
10.1. Strunjire
degrosare contur exterior cu respectarea cotelor
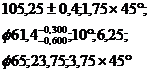
|
S22
|

|
4
|
10.2. Strunjire
degrosare exterioara 
|
4
|

|
10.2. Strunjire
degrosare exterioara 
|
S23
|
8
|
1,75
|
10.1. Strunjire
degrosare contur exterior cu respectarea cotelor
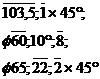
|
1,75
|
6,25
|
10.1. Strunjire
degrosare contur exterior cu respectarea cotelor
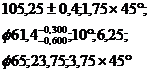
|
S24
|
1x45°
|
1,2
|
10.5. Strunjire
contur interior cu respectarea cotelor 
|
1,2
|
1,75x45°
|
10.5. Strunjire
contur interior cu respectarea cotelor 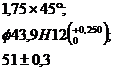
|
S25
|
51
|
1,75
|
10.5. Strunjire
contur interior cu respectarea cotelor 
|
1,75
|

|
10.5. Strunjire
contur interior cu respectarea cotelor 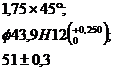
|
4.2.4.
Regimuri de prelucrare
Durabilitatea economica a sculei (T), parametrii regimului de
aschiere (t, t, s, s, v) si parametrii de reglare ai masinii
unelte (n, w) s-au determinat prin alegere din normative sau prin calcul, avand
in vedere si gamele de turatii si avansuri ale masinii
unelte, dupa cum urmeaza
a. Fazele de tip strunjire
Tabelul 4.2.4.1
PT
|
Faza
|
T, min
|
Ak,
mm
|
i
|
t, mm
|
s, mm / rot
|
d, mm
|
Viteza de
aschiere calculata / aleasa v0, m/min
|
Turatia
piesei, n, rot/min
|
Viteza de
aschiere reala, v, m/min
|
calculata
|
reala
|
PT1
|
10.1. Strunjire degrosare contur exterior cu
respectarea cotelor
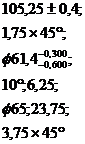
|
90
|
1,75
1,2
1,05
1,2
1,75
1,75
1,75
2,6
|
1
|
1,75
1,2
1,05
1,2
1,75
1,75
1,75
2,6
|
0,4
|
42,558
58
61,5
57,4
57,465
65
6576
17
|
200,7
204
210
207
202
190
202
175
|
1101..1503
1119
1088
1148
989.1120
930
846989
733
|
1101..1503
1119
1088
1148
989.1120
930
846989
733
|
200,7
204
210
207
202
190
202
175
|
10.2. Strunjire
degrosare exterioara 
|
60
|
4
|
1
|
4
|
0,08
|
56
|
48
|
273
|
273
|
48
|
10.3. Strunjire
cilindrica exterioara de semifinisare la 
|
90
|
0,5
|
1
|
0,5
|
0,20
|
60,4
|
303
|
1597
|
1597
|
303
|
10.4. Strunjire
cilindrica exterioara de finisare la 
|
90
|
0,2
|
1
|
0,2
|
0,12
|
60
|
350
|
1897
|
1897
|
350
|
10.5. Strunjire
contur interior cu respectarea cotelor 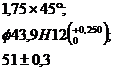
|
60
|
1,2
1,0
1,75
|
1
|
1,2
1,0
1,75
|
0,4
|
43,9
43,9
043,9
|
150
155
202
|
1087
1124
1465..5000
|
1087
1124
1465..5000
|
150
155
202
|
10.6. Strunjire
cilindrica interioara de semifinisare la 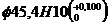
|
60
|
0,75
|
1
|
0,75
|
0,20
|
45,4
|
215
|
1057
|
1057
|
215
|
10.7.
Gaurire Ψ16
|
22
|
4
|
1
|
4
|
0,10
|
16
|
10,6
|
212
|
212
|
10,6
|
10.8. Filetare
interioara M48x2
|
60
|
1,099
0,20
|
7
2
|
0,174
0,10
|
2
|
48
|
44
|
292
|
292
|
44
|
20.1. Strunjire degrosare contur exterior cu respectarea
cotelor
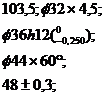 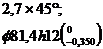
|
90
|
1,75
1,75
1,25
0,9
1,75
1,9
1,05
|
1
|
1,75
1,75
1,25
0,9
1,75
1,9
1,05
|
0,4
|
16.32
32
36
36.44
44.76
81,4
81,4
|
202
190
200
230
202
186
210
|
2010..4020
1890
1768
1665..2034
846.1461
727
821
|
2010..4020
1890
1768
1665..2034
846.1461
727
821
|
202
190
200
230
202
186
210
|
20.2. Strunjire
cilindrica exterioara de semifinisare la 
|
90
|
0,5
|
1
|
0,5
|
0,20
|
35
|
303
|
2755
|
2755
|
303
|
20.3. Strunjire
cilindrica exterioara de semifinisare la 
|
90
|
0,7
|
1
|
0,7
|
0,2
|
80
|
290
|
1154
|
1154
|
290
|
20.4. Strunjire
conica interioara de degrosare la 4,5x30°
|
60
|
2,25
|
1
|
2,25
|
0,4
|
21,2
|
135
|
2027
|
2027
|
135
|
20.5. Filetare
exterioara M35x1,5
|
90
|
0,874
0,10
|
7
3
|
0,124
0,033
|
1,5
|
35
|
58
|
527
|
527
|
58
|
20.6. Filetare
exterioara M80
|
90
|
2,768
0,25
|
11
4
|
0,243
0,062
|
4,5
|
80
|
53
|
211
|
211
|
53
|
PT2
|
20.1. Strunjire
frontala de degrosare la 106,5
|
90
|
3
|
1
|
3
|
0,384
|
85
|
189
|
707,7
|
710
|
189,5
|
20.2. Strunjie
cilindrica exterioara de degrosare la Ψ36h12
|
90
|
24,5
|
10
|
2,45
|
0,4
|
36
|
180
|
1591,5
|
1410
|
159,4
|
20.3. Strunjire
cilindrica exterioara de degrosare la Ψ32x4,5
|
90
|
2
|
1
|
2
|
0,4
|
32
|
186
|
1850,1
|
1910
|
192
|
20.4. Strunjire
frontala de degrosare la 48
|
90
|
2
|
1
|
2
|
0,384
|
85
|
205
|
767,6
|
710
|
189,5
|
20.5. Strunjire
degajare frontala Ψ44 / 2x60°
|
90
|
2
|
1
|
2
|
0,384
|
44
|
205
|
1483
|
1410
|
194,9
|
20.6.
Tesire exterioara 4,5x45°
|
90
|
3,15
|
1
|
3,15
|
0,4
|
85
|
178
|
666,5
|
710
|
189,5
|
20.7.
Gaurire Ψ16
|
22
|
8
|
1
|
8
|
0,10
|
16
|
10,6
|
212
|
250
|
12,5
|
20.8. Strunjire
conica interioara de degrosare la 4.5x30°
|
60
|
2,25
|
1
|
2,25
|
0,4
|
21,2
|
135
|
2027
|
1910
|
127,2
|
30.1. Strunjire
frontala de degrosare la 103,5
|
90
|
10
|
5
|
2
|
0,384
|
85
|
189
|
707,7
|
710
|
189,5
|
30.2. Strunjire
cilindrica exterioara de degrosare la Ψ65
|
90
|
10
|
5
|
2
|
0,4
|
65
|
186
|
910,8
|
1000
|
204,2
|
30.3. Strunjire
cilindrica exterioara de degrosare la 
|
90
|
1,8
|
1
|
1,8
|
0,4
|
61,4
|
190
|
984,9
|
1000
|
192,8
|
30.4. Strunjire
frontala de degrosare la 8
|
90
|
2
|
1
|
2
|
0,384
|
85
|
205
|
767,6
|
710
|
189,5
|
30.5. Strunjire
cilindrica exterioara de degrosare la Ψ81,4412
|
90
|
1,8
|
1
|
1,8
|
0,4
|
81,4
|
190
|
742,9
|
710
|
181,5
|
30.6. Strunjire
de degajare exterioara 5x10°
|
90
|
1,7
|
1
|
1,7
|
0,4
|
58,2
|
192
|
1050
|
1000
|
182,8
|
30.7. Strnjire
degajare exterioara Ψ56/60°
|
60
|
4
|
1
|
4
|
0,084
|
56
|
48
|
273
|
250
|
43,9
|
30.8.
Tesire exterioara 1,7x45° (la Ψ61,4)
|
90
|
1,2
|
1
|
1,2
|
0,4
|
61,4
|
198
|
1027
|
1000
|
192,9
|
30.9.
Tesire exterioara 2,7x45° (la Ψ81,4)
|
90
|
1,9
|
1
|
1,9
|
0,4
|
81,4
|
190
|
742,9
|
710
|
181,5
|
30.10.
Largire Ψ40
|
30
|
12
|
1
|
12
|
0,22
|
40
|
13,3
|
106
|
90
|
11,3
|
30.11. Strunjire
cilindrica interioara de degrosare la Ψ43,9H12
|
60
|
1,9
|
1
|
1,9
|
0,4
|
43,9
|
140
|
1015,1
|
1000
|
137,9
|
30.12. Strunjire
frontala de degrosare la S1
|
60
|
2
|
1
|
2
|
0,384
|
43,9
|
205
|
1486,4
|
1410
|
194,4
|
30.13.
Tesire interioara 1,75x45°
|
60
|
1,2
|
1
|
1,2
|
0,4
|
43,9
|
216
|
1566,1
|
1410
|
194,4
|
40.1. Strunjire
cilindrica exterioara de semifinisare la 
|
90
|
0,5
|
1
|
0,5
|
0,2
|
60,4
|
303
|
1597
|
1410
|
267,5
|
40.2. Strunjire
cilindrica exterioara de semifinisare la 
|
90
|
0,2
|
1
|
0,2
|
0,12
|
60
|
350
|
1857
|
1910
|
360
|
40.3. Strunjire
cilindrica exterioara de semifinisare la Ψ80h10
|
90
|
0,7
|
1
|
0,7
|
0,2
|
80
|
290
|
1154
|
1000
|
251,3
|
40.4. Filetare
exterioara M80
|
90
|
2,67
0,25
|
11
4
|
0,24
0,06
|
4,5
|
80
|
53
|
211
|
180
|
45,2
|
40.5. Strunjire
cilindrica interioara de semifinisare la Ψ45,4H10
|
60
|
0,75
|
1
|
0,75
|
0,2
|
45,4
|
210
|
1472,3
|
1410
|
199,7
|
40.6. Filetare
interioara M48x2
|
60
|
1,099
0,20
|
7
2
|
0,157
0,10
|
2
|
48
|
44
|
292
|
250
|
37,7
|
50.1. Strunjire
cilindrica exterioara de semifinisare la Ψ35h10
|
90
|
0,5
|
1
|
0,5
|
0,2
|
35
|
303
|
2755
|
2800
|
307,8
|
50.2. Filetare
exterioara M35x1,5
|
90
|
0,874
0,10
|
7
3
|
0,124
0,033
|
1,5
|
35
|
58
|
527
|
500
|
54,9
|
b. Fazele de tip frezare
Tabelul 4.2.4.2.
PT
|
Faza
|
T, min
|
t, mm
|
Viteza de avans
vs , mm/min
|
Viteza de
aschiere calcultata / aleasa v0, m/min
|
Turatia
sculei, n, rot/min
|
Viteza de
aschiere reala, v, m/min
|
calculata
|
reala
|
PT 1
|
30.1.Frezare
canal 
|
90
|
12
|
190
|
35,8
|
950
|
950
|
35,8
|
30.2.Frezare
canal 
|
30.3.Frezare
canal 
|
40.1.
|
120
|
5
|
190
|
141,3
|
450
|
475
|
149,2
|
PT 2
|
60.1. Frezare
canal 
|
90
|
12
|
190
|
35,8
|
950
|
950
|
35,8
|
60.2.
|
60.3.
|
70.1. Frezare
laturi S = 55
|
120
|
5
|
190
|
141,3
|
450
|
475
|
149,2
|
Viteza de aschiere se calculeaza cu formula :
[m/min] ; unde
Cv = 294 (tab. 10.30[5])
M = exponentul durabilitatii ; m = 0,125 (tab. 10.29[5])
HB = duritatea materialului piesei ; HB = 229
xv, yv = exponentii adancimii de
aschiere si al avansului ; xv = 0,18 ; yv =
0,35 (tab. 10.30[5])
n = exponentul duritatii materialului de prelucrat ; n =
1,75 (pentru otel carbon cu HB > 130)
k1 = coeficient functie de sectiunea
transversala a cutitului ;
; unde :
q = aria sectiunii transversale a cutitului; q = 20*20 = 400
mm2
ξ = coeficient functie de materialul de prelucrat; ξ =
0,08 → 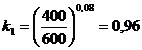
k2 = coeficient functie de inghiul de atac principal (
), k2=
; unde:
ρ = exponent functie de materialul prelucrat; ρ = 0,3
(pentru otel prelucrat cu carbura metalica)
k2 =
(45/5)0,3 = 1,39
K3 = coeficient functie de unghiul de atac secundar (
); k3 =
(a/
)0,09; unde :
a = 15 (pentru scule cu placute dure)
k3 = (15/95)0,09 = 0,84
k4 = coeficient functie de raza de racordare a
varfului cutitului (r=0,8mm)
k4 = (r/2)μ ; unde : μ = exponent
functie de tipul prelucrarii si a materialului prelucrat
μ = 0,1 pentru prelucrarea de degrosare
k4 =
(0,8/2)0,1=0,91
k5 = coeficient functie de partea aschietoare a
sculei; k5 = 0,7 (tab. 10.31[5])
k6 = coeficient functie de materialul prelucrat; k6
= 1,1 (tab. 10.32[5])
k7 = coeficient functie de modul de obtinere a
semifabricatului; k7 = 0,9 (pentru materiale recoapte)
k8 = coeficient functie de starea stratului
superficial al semifabricatului; k8 = 1,0 (pentru otel cu
tunder)
k9 = coeficient functie de forma suprafetei de
degajare a cutitului; k9 = 1,15 (pentru fata de degajare
cu fateta)
k10 = coeficient functie de schema de aschiere; k10
= 1,5 (tab. 10.34[5])

= 200,7 m/min
Turatia calculata a piesei va fi:

Verificarea puterii
Componenta principala (tangentiala) a fortei de
aschiere Pz = 70 daN (tab. 9.25[1])
Puterea reala consumata va fi:
; η = randamentul mecanic; η = 0,8
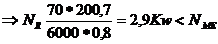
Prelucrarea acestei
suprafete se poate executa pe masina unealta aleasa cu
parametrii reali ai regimului de aschiere steabiliti anterior.
Suprafata
S14 : v = 204 m/min (tab. 9.15.[1])
rot/min.
Suprafata
S13 : v = 210 m/min (tab. 9.15[1])
rot/min .
Suprafata
S17 : v = 207 m/min (tab. 9.15.[1])
rot/min .
Suprafata
S23 : v = 202 m/min (tab. 9.25[1])
rot/min.
Suprafata
S21 : v = 190 m/min (tab. 9.15[1])
rot/min.
Suprafata
S18 : v = 202 m/min (tab. 9.25[1])
.
Suprafata
S12 : v = 175 m/min (tab. 9.15[1])
rot/min.
Faza 10.2. Strunjire degajare exterioara Ψ56/60° [1]
t = Ap = 4 mm .
Tec = 60 min (tab. 9.10)
S = 0,08 mm/rot (tab. 9.30)
v = 48 m/min (tab. 9.30)
rot/min .
Faza 10.3. Strunjire cilindrica exterioara de semifinisare
la
[1]
t = Apsemifinisare = 9,5 mm
Tec = 90 min
S = 0,150,24 mm/rot (tab. 9.8.) . Se considera S = 0,2 mm/rot
.
v = 303 m/min (tab. 9.15.)
rot/min.
Faza 10.4. Strunjire cilindrica exterioara exterioara
de finisare la
[1]
t = Apfinisare = 0,2 mm
Tec = 90 min
S = 0,100,15 mm/rot
mm/rot.
v = 350 rot/min
rot/min .
Faza 10.5. Strunjire degrosare contur interior cu respectarea
cotelor 1,75x45° ;
si 51±0,3 [1]
t = Ap = 1,2 mm S24
1,0
mm S16
1,75 mm S25
Tec = 60 mm (tab. 9.10.)
S = 0,30,5 mm/rot
S = 0,4 mm/rot.
Suprafata
S24 : v = 150 m/min (tab. 9.20)
rot/min.
Suprafata
S16 : v = 155 m/min (tab. 9.20)
rot/min.
Suprafata
S25 : v = 202 m/min (tab. 9.25)
;obs: n = 5000 = turatia maxima a masinii
unealta .
Faza 10.6. Strunjire cilindrica interioara de semifinisare
la
[1]
t = Apsemifinisare = 0,76 mm
Tec = 60 min
S = 0,15.0,24 mm/rot
mm/rot .
v = 215 m/min
rot/min.
Faza 10.7. Gaurire Ψ16 [1]
t = Ap = 8 mm
Tec = 22 min (tab. 9.113)
S = 0,10 mm/rot
n = 212 rot/min
m/min.
Faza 10.8. Filetare interioara M48x2 [1]
Aptotal = 1,299 mm
S = p = 2 mm/rot (tab. 9.113)
Din tab.9.29 se aleg :
S =
0,10 mm/rot
n =
212 rot/min
m/min.
Faza 10.8. Filetare interioara M48x2 [1]
Aptotal = 1,299 mm
S = p = 2 mm/rot (p = pasul filetului)
Din tab. 9.32. se
aleg :
Apdegr = 1,099 mm
Apfinis = 0,20 mm
id = 7 treceri
if = 2 treceri
mm/trecere
mm/trecere
rot/min .
Faza 20.1. Strunjire degrosare contur exterior cu respectarea
cotelor 
t = Ap = 1,75 mm S6
1,75 mm S4
1,25 mm S3
0,9 mm S2
1,75 mm S9
1,9 mm S10
1,05 mm S11
Tec = 90 min
S = 0,30,5 mm/rot
S = 0,4 mm/rot
-Suprafata S6 : v = 202 m/min
rot/min .
Suprafata S4 : v = 190 m/min
rot/min .
Suprafata
S3 : v = 200 m/min
rot/min .
Suprafata
S2 : v = 230 m/min 
Suprafata
S9 : v = 202 m/min 
Suprafata
S10 : v = 186 m/min
rot/min.
Suprafata
S11 : v = 210 m/min
rot/min.
Faza 20.2. Strunjire cilindrica
exterioara de semifinisare la
[1]
t = Apsemifinisare = 0,5 mm
Tec = 90 min
S = 0,15..0,24 mm/rot
S = 0,20 mm/rot.
v = 303 m/min
rot/min.
Faza 20.3. Strunjire cilindrica
exterioara de semifinisare la
[1]
t = Apsemifinisare = 2,25 mm
Tec = 90 min
S = 0,20 mm/rot
v = 290 m/min
rot/min.
Faza 20.4. Strunjire conica interioara de
degrosare la 4,5x30°[1]
t = Ap = 2,25 mm
Tec = 60 min
S = 0,4 mm/rot
v = 135 m/min
rot/min.
Faza 20.5. Filetare exterioara M35x1,5 [1]
Aptotal = 0,974 mm
Tec = 90 min
S = p = 1,5 mm/rot
Apd = 0,874 mm
Apt = 0,10 mm
id = 7 treceri
td = 0,874/7 = 0,124 mm/trecere
it = 3 treceri
tf = 0,10/3
= 0,033 mm/trecere
v = 58 m/min
rot/min.
Faza 20.6. Filetare exterioara M80 [1]
Aptotal = 2,923 mm
Tec = 90 min
S = p = 4,5 mm/rot
Apd = 2,678 mm
Apf = 0,25 mm
id = 11 treceri
td = 2,678/11 = 0,243 mm/trecere
if = 4 treceri
tf = 0,25/4
= 0,062 mm/trecere
v = 53 m/min
rot/min .
Faza 30.1. Frezare canal
[2]
t = Ap = 12 mm
Tec = 90 min (tab. 9.29)
te = 12 mm = Dfreza
Din tab. 11.25. se aleg :
vs
= 210 mm/min
vsr = 190
mm/min
n =
950 rot/min
nr = 950
rot/min
m/min
Faza 30.2. Frezare canal
[2]
t = Ap = 12 mm
Tec = 90 min (tab. 9.29)
te = 12 mm = Dfreza
Din tab. 11.25. se aleg :
vs
= 210 mm/min
vsr = 190
mm/min
n = 950 rot/min
nr = 950
rot/min
m/min
Faza 30.3. Frezare canal
[2]
t = Ap = 12 mm
Tec = 90 min (tab. 9.29)
te = 12 mm = Dfreza
Din tab. 11.25. se aleg :
vs
= 210 mm/min
vsr = 190
mm/min
n = 950 rot/min
nr = 950
rot/min
m/min
Faza 40.1. Frezare laturi S = 55 [2]
t = Ap = 2,5 + 2,5 = 5 mm
Tec = 120 min
te = 25,5 mm
Din tab. 11.43. se aleg :
vs
= 190 mm/min
vsr = 190
mm/min
n =
450 rot/min
nr = 475
rot/min
m/min .
4.2.2.5. Normele de timp
Orice nivel de operatie, norma de timp are expresia :
Tr = Tu + Tpi/no
Tu = Tb + Ta + Tdt
+ Tdo + Ton + Tpi/no [mm/buc]
Th = ΣThk ;
; w = n∙s sau se
Ta = Ta1 + Σ(Ta2 + Ta3
+ Ta4)k , Top = Ta + Tb
;
unde:
Tu timpul unitar
Tpi timpul de pregatire incheiere a locului de
munca
no numarul de piese din lotul care urmeaza a fi
prelucrat
Th timpul de baza , Ta timpul auxiliar
Tdt timpul de deservire tehnica, Tdo
timpul de deservire organizatorica,
Td timpul de deservire a locului de munca
Ton timpul de odihna si necesitati
firesti
Ta1 timp de prindere si desprindere
Ta2 timp auxiliar de comanda
Ta3 timp auxiliar de reglare
Ta4 timp auxiliar de control
Top timp operativ
k numarul de ordine faza de prelucrare
lmax lungimea maxima a suprafetei de prelucrat
l1,l2 curse de siguranta la intrare
si, respectiv, la iesire
i numar de treceri
w viteza de avans .
Se adopta no = 100 bucati
Elementele componenteale normei de timp pentru fiecare operatie
s-au determinat fie prin calcul, fie prin alegere din normative si sunt
prezentate mai jos:
a)
Operatia 10. Strunjire I
1. Timpul de pregatire incheiere Tpi
= 12 + 10 + 13 = 35 min .
2. Elementele de calcul pentru Tb
si Ta sunt prezentate in tabelul de mai jos :
Nr. si denumirea
fazei
|
l mm
|
l1 mm
|
l2 mm
|
i-
|
tb mm
|
ta1
mm
|
ta2
mm
|
ta3
mm
|
ta4
mm
|
a+b Prindere -
desprindere piesa
|
|
|
|
|
|
0,2
|
|
|
|
10.1.
|
57,55
|
1
|
1
|
1
|
0,14
|
|
0,03
|
0,25
|
0,3
|
10.2.
|
4,5
|
1
|
0
|
1
|
0,25
|
|
0,03
|
0,1
|
0,07
|
10.3.
|
19,5
|
1
|
1
|
1
|
0,07
|
|
0,03
|
0,1
|
0,07
|
10.4.
|
19,5
|
1
|
1
|
1
|
0,09
|
|
0,03
|
0,15
|
0,2
|
10.5.
|
75,4
|
1
|
1
|
1
|
0,16
|
|
0,03
|
0,2
|
0,15
|
10.6.
|
38
|
1
|
0
|
1
|
0,18
|
|
0,03
|
0,1
|
0,07
|
10.7.
|
54,25
|
4,6
|
1,5
|
1
|
2,85
|
|
0,03
|
0,07
|
0,07
|
10.8.
|
38
|
1
|
0
|
9
|
0,6
|
|
0,03
|
0,15
|
0,2
|
[min]

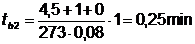
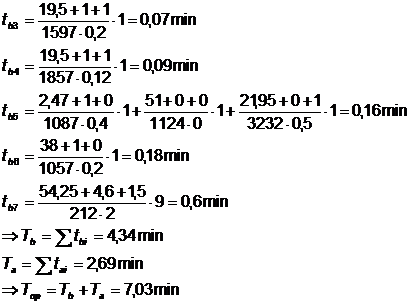
3. Tdt si Ton
Tdt = Tb∙2/100 = 0,087 min ; Tdo
= Top∙1/100 = 0,07 min
Td = Tdt + Tdo = 0,16 min
Ton = Top ∙3,5/100 = 0,25 min
4. Timpul unitar
Tu = Top + Td + Ton = 7,44
min
In concluzie : Tu =
7,44 min/buc ; Tn = 7,79 min/buc .
b)
Operatia 20. Strujire II
1. Timpul de pregatire inchidere Tpi
= 35 min .
2. Elementele de calcul pentru Tb
si Ta sunt prezente in tabelul de mai jos :
Nr. si
denumirea fazei
|
l mm
|
l1 mm
|
l2 mm
|
i-
|
tb mm
|
ta1
mm
|
ta2
mm
|
ta3
mm
|
ta4
mm
|
a+b Prindere -
desprindere piesa
|
|
|
|
|
|
0,2
|
|
|
|
20.1.
|
104,6
|
1
|
1
|
1
|
0,19
|
|
0,03
|
0,25
|
0,3
|
20.2.
|
45,5
|
1
|
0
|
1
|
0,08
|
|
0,03
|
0,1
|
0,07
|
20.3.
|
18
|
1
|
1
|
1
|
0,09
|
|
0,03
|
0,1
|
0,07
|
20.4.
|
5,2
|
1
|
1
|
1
|
0,009
|
|
0,03
|
0,1
|
0,07
|
20.5.
|
44
|
1,5
|
0
|
10
|
0,58
|
|
0,03
|
0,15
|
0,2
|
20.6.
|
18
|
1,5
|
2
|
15
|
0,34
|
|
0,03
|
0,15
|
0,2
|
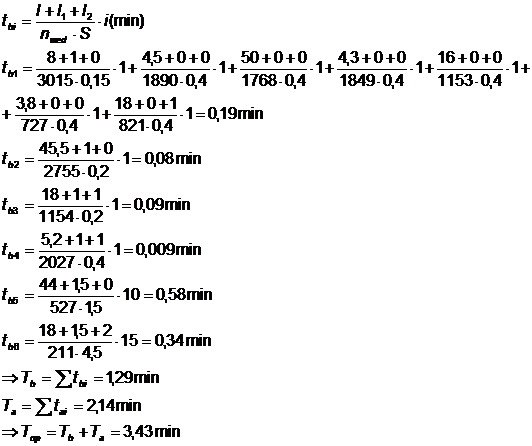
3. Td si Tn
Tdt = Tb∙2/100 = 0,026 min; Tdo
= Top∙1/100 = 0,034 min
Td = Tdt
+ Tdo = 0,06 min .
Ton = Top∙3,5/100 = 0,12 min .
4. Timpul unitar Tu = Top
+ Td + Ton = 3,61 min
In concluzie : Tu =
3,61 min/buc; Tn = 3,96 min/buc.
c)
Operatia 30 Frezare I
1. Timpul de pregatire inchidere Tpi
= 10 + 14 = 24 min
2. Elementele de calcul pentru Tb
si Ta sunt prezente in tabelul de mai jos :
Nr. si
denumirea fazei
|
l mm
|
l1 mm
|
l2 mm
|
i-
|
tb mm
|
ta1
mm
|
ta2
mm
|
ta3
mm
|
ta4
mm
|
a+b+c+d Prindere
indexari desprindere piesa
|
|
|
|
|
|
1,3
|
|
|
|
30.1.
|
35
|
2,7
|
0
|
1
|
0,19
|
|
0,2
|
0,15
|
0,15
|
30.2.
|
35
|
2,7
|
0
|
1
|
0,19
|
|
0,2
|
0,15
|
0,15
|
30.3.
|
35
|
2,7
|
0
|
1
|
0,19
|
|
0,2
|
0,15
|
0,15
|

3. Td si Ton
Tdt = Tb ∙ 5/100 = 0,029 min; Tdo
= Top∙1,2/100 = 0,04 min
Td = Tdt + Tdo = 0,069 min;
Ton = Top∙3/100 = 0,1 min
4. Timpul unitar Tu = Top
+ Td + Ton = 3,54 min
In concluzie : Tu = 3,54 min/buc; Tn = 3,78
min/buc.
d)
Operatia 40 Frezare II
1. Timpul de pregatire inchidere Tpi
= 24 min
2. Elementele de calcul pentru Tb
si Ta sunt prezente in tabelul de mai jos :
Nr. si
denumirea fazei
|
l mm
|
l1 mm
|
l2 mm
|
i-
|
tb mm
|
ta1
mm
|
ta2
mm
|
ta3
mm
|
ta4
mm
|
a + b Prindere
desprindere piesa
|
|
|
|
|
|
0,8
|
|
|
|
40.1.
|
24,3
|
12
|
2
|
1
|
0,2
|
|
0,2
|
0,2
|
0,15
|

3. Td si Ton
Tdt = Tb ∙ 5/100 = 0,010 min; Tdo
= Top ∙ 1,2/100 = 0,018 MIN
Td = Tdt
+ Tdo = 0,028 min
Ton = Top ∙ 3/100 = 0,046 min
4. Timpul unitar Tu=Top+Td+Ton=1,62
min
In concluzie: Tu = 1,62 min/buc; Tn = 1,86 min/buc
.
PT2
a) Operatia 10 Debitare
1. Timpul de pregatire inchidere Tpi
= 12 + 18 = 30 min.
2. Elementele de calcul pentru Tb
si Ta sunt prezentate in tabelul de mai jos :
Nr. si
denumirea fazei
|
l mm
|
l1 mm
|
l2 mm
|
i-
|
tb mm
|
ta1
mm
|
ta2
mm
|
ta3
mm
|
ta4
mm
|
a + b Prindere
desprindere piesa
|
|
|
|
|
|
0,15
|
|
|
|
10.1.
|
85
|
3
|
2
|
1
|
2
|
|
0,02
|
0,1
|
0,07
|
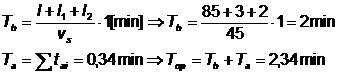
3. Td si Ton
Tdt = Tb ∙ 5/100 = 0,01 min; Tdo
= Top ∙ 1,2/100 = 0,028 MIN
Td = Tdt
+ Tdo = 0,128 min
Ton = Top ∙ 3/100 = 0,07 min
4. Timpul unitar Tu = Top +
Td + Ton = 2,54 min
In concluzie Tu = 2,54 min/buc; Tn = 2,84 min/buc.
b)
Operatia 20 Strunjire I (degrosare)
1. Timpul de pregatire incheiere Tpi
= 10 + 10 = 20 min .
2. Elementele de calcul pentru Tb
si Ta sunt prezente in tabelul de mai jos :
Nr. si
denumirea fazei
|
l mm
|
l1 mm
|
l2 mm
|
i-
|
tb mm
|
ta1
mm
|
ta2
mm
|
ta3
mm
|
ta4
mm
|
a + b Prindere
desprindere piesa
|
|
|
|
|
|
0,5
|
|
|
|
20.1
|
85
|
1
|
1
|
1
|
0,32
|
|
0,15
|
0,1
|
0,07
|
20.2
|
48
|
1
|
0
|
10
|
0,82
|
|
0,15
|
0,1
|
0,07
|
20.3.
|
4,5
|
1
|
0
|
1
|
0,06
|
|
0,15
|
0,1
|
0,07
|
20.4.
|
24,5
|
1
|
0
|
1
|
0,09
|
|
0,15
|
0,1
|
0,07
|
20.5.
|
4,5
|
1
|
0
|
1
|
0,01
|
|
0,15
|
0,1
|
0,07
|
20.6
|
4,5
|
1
|
0
|
1
|
0,17
|
|
0,15
|
0,1
|
0,07
|
20.7.
|
106,5
|
4,6
|
1,5
|
1
|
4,87
|
|
0,15
|
0,1
|
0,07
|
20.8.
|
5,2
|
1
|
1
|
1
|
0,009
|
|
0,15
|
0,1
|
0,07
|
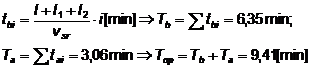
3. Td si Ton
Tdt = Tb ∙ 2/100 = 0,13 min; Tdo
= Top ∙ 1/100 = 0,094 min
Td = Tdt
+ Tdo = 0,22 min
Ton = Top ∙ 3,5/100 = 0,33 min
4. Timpul unitar Tu = Top +
Td + Ton = 9,96
min
In concluzie Tu = 9,96 min/buc; Tn = 10,16 min/buc.
c) Operatia 30.
Strunjire II (degrosare)
1. Timpul de pregatire incheiere Tpi
= 10 + 10 = 20 min .
2. Elementele de calcul pentru Tb
si Ta sunt prezente in tabelul de mai jos :
Nr. si
denumirea fazei
|
l mm
|
l1 mm
|
l2 mm
|
i-
|
tb mm
|
ta1
mm
|
ta2
mm
|
ta3
mm
|
ta4
mm
|
a + b Prindere
desprindere piesa
|
|
|
|
|
|
0,5
|
|
|
|
30.1.
|
85
|
1
|
1
|
1
|
0,32
|
|
0,15
|
0,1
|
0,07
|
30.2
|
33,5
|
1
|
0
|
5
|
0,45
|
|
0,15
|
0,1
|
0,07
|
30.3.
|
25,5
|
1
|
0
|
1
|
0,07
|
|
0,15
|
0,1
|
0,07
|
30.4.
|
1,8
|
1
|
0
|
1
|
0,009
|
|
0,15
|
0,1
|
0,07
|
30.5.
|
20
|
1
|
10
|
1
|
0,08
|
|
0,15
|
0,1
|
0,07
|
30.6
|
5
|
1
|
0
|
1
|
0,01
|
|
0,15
|
0,1
|
0,07
|
30.7.
|
12,7
|
1
|
0
|
1
|
0,62
|
|
0,15
|
0,1
|
0,07
|
30.8.
|
1,7
|
1
|
0
|
1
|
0,007
|
|
0,15
|
0,1
|
0,07
|
30.9.
|
2,7
|
1
|
0
|
1
|
0,01
|
|
0,15
|
0,1
|
0,07
|
30.10.
|
46
|
11,5
|
0
|
1
|
2,67
|
|
0,15
|
0,1
|
0,07
|
30.11.
|
51
|
1
|
0
|
1
|
0,13
|
|
0,15
|
0,1
|
0,07
|
30.12.
|
13,9
|
1
|
0
|
1
|
0,03
|
|
0,15
|
0,1
|
0,07
|
30.13.
|
1,75
|
1
|
1
|
1
|
0,006
|
|
0,15
|
0,1
|
0,07
|

3. Td si Ton
Tdt = Tb ∙ 2/100 = 0,088 min; Tdo
= Top ∙ 1/100 = 0,091 min
Td = Tdt
+ Tdo = 0,18 min
Ton = Top ∙ 3,5/100 = 0,32 min .
4. Timpul unitar Tu = Top +
Td + Ton = 9,57
min
In concluzie : Tu = 9,57 min/buc; Tn = 9,77 min/buc.
d) Operatia 40 Strunjire
III (finisare)
1. Timpul de pregatire incheiere Tpi
= 10 + 10 = 20 min .
2. Elementele de calcul pentru Tb
si Ta sunt prezente in tabelul de mai jos :
Nr. si
denumirea fazei
|
l mm
|
l1 mm
|
l2 mm
|
i-
|
tb mm
|
ta1
mm
|
ta2
mm
|
ta3
mm
|
ta4
mm
|
a + b Prindere
desprindere piesa
|
|
|
|
|
|
0,5
|
|
|
|
40.1
|
19,5
|
1
|
1
|
1
|
0,07
|
|
0,15
|
0,15
|
0,1
|
40.2
|
19,5
|
1
|
1
|
1
|
0,09
|
|
0,15
|
0,2
|
0,15
|
40.3.
|
18
|
1
|
1
|
1
|
0,09
|
|
0,15
|
0,15
|
0,1
|
40.4.
|
18
|
1,5
|
1,5
|
1,5
|
0,35
|
|
0,15
|
0,2
|
0,2
|
40.5.
|
38
|
1
|
0
|
1
|
0,14
|
|
0,15
|
0,15
|
0,1
|
40.6
|
38
|
1
|
0
|
10
|
0,07
|
|
0,15
|
0,2
|
0,2
|
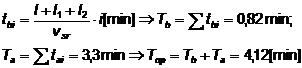
3. Td si Ton
Tdt = Tb ∙ 2/100 = 0,016 min; Tdo
= Top ∙ 1/100 = 0,041 min
Td = Tdt
+ Tdo = 0,057 min
Ton = Top ∙ 3,5/100 = 0,144 min .
4. Timpul unitar Tu = Top +
Td + Ton = 4,32
min
In concluzie : Tu = 4,32 min/buc; Tn = 4,52 min/buc.
e)
Operatia 50 Strunjire IV (finisare)
1. Timpul de pregatire incheiere Tpi
= 10 + 10 = 20 min .
2. Elementele de calcul pentru Tb
si Ta sunt prezente in tabelul de mai jos :
Nr. si
denumirea fazei
|
l mm
|
l1 mm
|
l2 mm
|
i-
|
tb mm
|
ta1
mm
|
ta2
mm
|
ta3
mm
|
ta4
mm
|
a + b Prindere
desprindere piesa
|
|
|
|
|
|
0,5
|
|
|
|
50.1
|
43,5
|
1
|
0
|
1
|
0,08
|
|
0,15
|
0,15
|
0,1
|
50.2
|
39,5
|
1
|
0
|
10
|
0,53
|
|
0,15
|
0,2
|
0,2
|
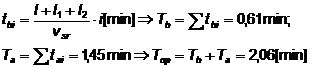
3. Td si Ton
Tdt = Tb ∙ 2/100 = 0,012 min; Tdo
= Top ∙ 1/100 = 0,021 min
Td = Tdt
+ Tdo = 0,033 min
Ton = Top ∙ 3,5/100 = 0,072 min .
4. Timpul unitar Tu = Top +
Td + Ton = 2,17
min
In concluzie : Tu = 2,17 min/buc; Tn = 2,37 min/buc.
f)
Operatia 60 Frezare I
1. Timpul de pregatire inchidere Tpi = 10 + 14 = 24
min
2. Elementele de calcul pentru Tb si Ta
sunt prezente in tabelul de mai jos :
Nr. si
denumirea fazei
|
l mm
|
l1 mm
|
l2 mm
|
i-
|
tb mm
|
ta1
mm
|
ta2
mm
|
ta3
mm
|
ta4
mm
|
a+b+c+d Prindere
indexari desprindere piesa
|
|
|
|
|
|
1,3
|
|
|
|
60.1.
|
35
|
2,7
|
0
|
1
|
0,19
|
|
0,2
|
0,15
|
0,15
|
60.2.
|
35
|
2,7
|
0
|
1
|
0,19
|
|
0,2
|
0,15
|
0,15
|
60.3.
|
35
|
2,7
|
0
|
1
|
0,19
|
|
0,2
|
0,15
|
0,15
|

3. Td si Ton
Tdt = Tb ∙ 5/100 = 0,029 min; Tdo
= Top∙1,2/100 = 0,04 min
Td = Tdt + Tdo = 0,069 min;
Ton = Top∙3/100 = 0,1 min
4. Timpul unitar Tu = Top + Td + Ton
= 3,54 min
In concluzie : Tu = 3,54 min/buc; Tn = 3,78
min/buc.
g)
Operatia 70 Frezare II
1. Timpul
de pregatire inchidere Tpi = 24 min
2. Elementele de calcul pentru Tb
si Ta sunt prezente in tabelul de mai jos :
Nr. si
denumirea fazei
|
l mm
|
l1 mm
|
l2 mm
|
i-
|
tb mm
|
ta1
mm
|
ta2
mm
|
ta3
mm
|
ta4
mm
|
a + b Prindere
desprindere piesa
|
|
|
|
|
|
0,8
|
|
|
|
40.1.
|
24,3
|
12
|
2
|
1
|
0,2
|
|
0,2
|
0,2
|
0,15
|

3. Td si Ton
Tdt = Tb ∙ 5/100 = 0,010 min; Tdo
= Top ∙ 1,2/100 = 0,018 MIN
Td = Tdt
+ Tdo = 0,028 min
Ton = Top ∙ 3/100 = 0,046 min
4. Timpul unitar Tu=Top+Td+Ton=1,62
min
In concluzie: Tu = 1,62 min/buc; Tn = 1,86
min/buc .
5.
Proiectare de echipament tehnologic
5.1.
Date initale specifice
Echipamentul proiectat este un dispozitiv de prelucrare utilizat in
cadrul operatiei 40 Frezare II PT1 si operatia Frezare II
PT2.
SOF 0 a fost determinat la capitolul 4 si este prezentata
in figura de mai jos:
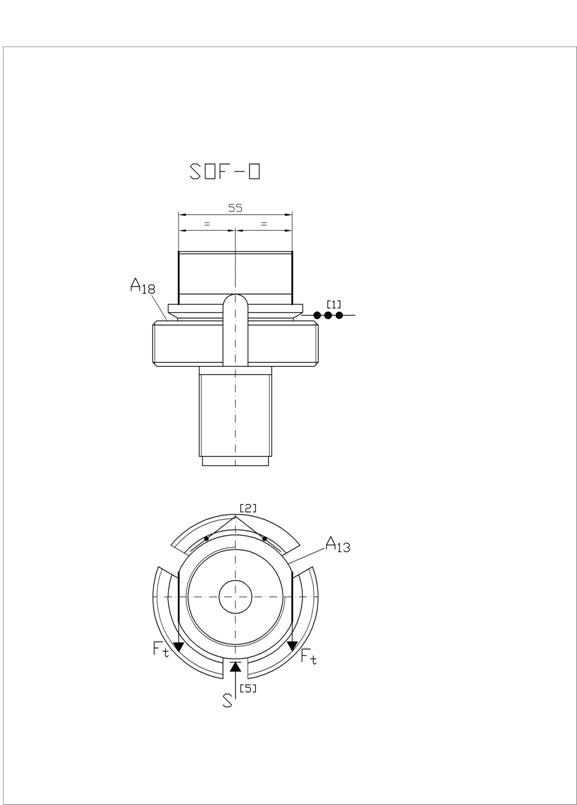
Cerinta economica :
cresterea productivitatii muncii .
Obiectiv principal : introducerea de echipament nou in vederea
reducerii costului de fabricare si a efortului fizic.
Calculul fortei de strangere S .
In timpul prelucrarii, componenta principala
(tangentiala) a fortei de aschiere Ft = 160 daN
isi schimba tot timpul directia si sensul

Exista pericolul ca Ft
sa se desprinda PSF de reazemul [2]
.
Se pune conditia S>Ft
S = kFt , k > 1.
Considerand k = 3
S = 3∙160 = 480 daN .
Descrierea unui ciclu complet de functionare .
Dispozitivul proiectat este instalat pe masa masinii
unealta fiind centrat cu cele doua pene (pozitia 11) si
fixat cu doua suruburi M12 pentru canale T .
Reglarea frezelor la cota se face cu gabaritul de reglare
pozitia 14 .
Pentru prelucrarea PSF se parcurg urmatoarele etape :
1. Se prinde PSF in dispozitiv astfel :


- orientarea PSF se face cu :
suprafetele inferioare ale prismei ,pozitia 1 , si ghidajului
,pozitia 7 ( ) si prisma scurta, pozitia
1( ) .
- strangerea PSF se face cu placa mobila, pozitia 2,
actionand cu o cheie fixa axul filetat, pozitia 4.
2. Se frezeaza cele 2 laturi ale PSF
cu un tren de freze disc .
3. Dupa toate prelucrarile, se slabeste axul, pozitia
4, si se scoate piesa din dispozitiv.
4. Se curata dispozitivul de aschii .
5. Se reia ciclul .
PT1
|
Tn
min/buc
|
PT2
|
Tn
min/buc
|
10. Strunjire I
|
7,79
|
10. Debitare
|
2,84
|
20. Strunjire II
|
3,96
|
20. Strunjire I
(degrosare)
|
10,16
|
30. Frezare I
|
3,78
|
30. Strunjire II
(degrosare)
|
9,77
|
40. Frezare II
|
1,86
|
40. Strunjire
III (finisare)
|
4,52
|
|
|
50. Strunjire IV
(finisare)
|
2,37
|
60. Frezare I
|
3,78
|
70. Frezare II
|
1,86
|
6.
Analiza economica
a) Expresia generala a costului de
fabricare
Costul de fabricare este :

unde :
C este costul de fabricare [RON]
X volumul de productie [buc.]
A costul de fabricare direct unitar(dependent de
produs/reper)[RON/buc]
B costul de fabricare indirect (independent de produs/reper) [RON].
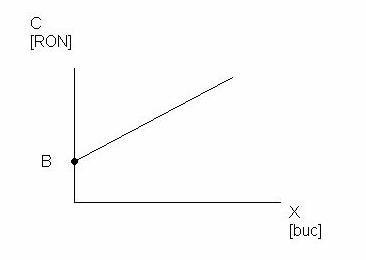
b) Expresia costului de fabricare direct
unitar
Costul de fabricare direct unitar, A [RON/buc], este
A = Cα
+ Cβ + Cγ + Cδ + Cη
+ Cθ
unde :
Cα costul
materialului consumat [RON/buc]
Cβ costul
manoperei [RON/buc]
Cγ costul
asigurarilor sociale [RON/buc]
Cδ costul
ajutorului de somaj [RON/buc]
Cη costul regiei
(pentru energie, substante de lucru, curatenie etc.) [RON/buc]
Cθ costul
amortizarii si reparatiilor capitale ale utilajelor [RON/buc] .
Costul materialului
consumat, Cα [RON/buc], este :
Cα
= mrcr + mdcd
unde :
mr este masa reperului
[kg/buc]
md este masa
deseurilor[RON/kg]
cr este costul unitar
al materialului reperului [RON/kg]
cd este costul unitar
al materialului deseurilor [RON/kg] .
Se recomanda :
cd = 0,5cr
mr = 0,90 kg
md1 ≈ 0,012 kg
md2 ≈ 4,03 kg
cr ≈ 3,0 RON/kg
cd ≈ 1,5 RON/kg
cd = 1,5
RON/kg ; cα1 = 2,71 RON ; cα2 = 8,74 RON/buc.
Costul manoperei, Cβ
[RON/buc], in conditiile in care toate activitatile din
operatie se efectueaza de acelasi operator, este
Cβ
= ΣTniSi/60
unde:
Tn este norma de timp
[min/buc]
S este salariul operatorului
[RON//ora]
i este numarul de ordine al
operatiei : i = 1,2,-----
Se recomanda: S1 =
4 8 RON/ora . Se considera Si = 6 RON/ora .
Cβ1 =
1,73 RON/buc ; Cβ2 = 3,53 RON/buc.
Costul asigurarilor sociale,
Cγ [RON/buc], este :
Cγ
= KγCβ/100
unde:
Kγ este o
cota procentuala [%]
Se recomanda; Kγ
= 25 45 . Se considera Kγ = 35 % .
Cγ1 = 0,60 RON/buc; Cγ2 =
1,23 RON/buc .
Costul ajutorului de somaj, Cδ
[RON/buc], este
Cδ
= KδCβ/100
unde:
Kδ este o
cota procentuala [%]
Se recomanda : Kδ
= 5 10 .
Se considera Kδ
= 8 %.
Cδ1 = 0,13 RON/buc; Cδ2 =
0,28 RON/buc.
Costul regiei, Cη
[RON/buc], este
Cη
= Kη(Cη + Cγ + Cδ)/100
unde:
Kη este o cota procentuala [%] .
Se recomanda: Kη
= 35 85 .
Se considera: Kη
= 50 % .
Cη1 = 1,23 RON/buc ; Cη2 =
2,52 RON/buc .
Costul amortizarii si
reparatiilor capitale ale utilajelor, Cθ [RON/buc], este :
Cθ
= ΣVui(1/Zui+Kui/100)Tni/(60Hui)
unde:
Vu este valoarea de
achizitie a utilajului [RON/buc], este :
Ku este o cota
procentuala privind reparatiile capitale [%];
Hu este numarul orelor de functionare
pe an [ore/an]
Zu este numarul
anilor de amortizare [ani]
Se recomanda: Zu =
5 10 ; Ku = 15 35 ; Hu = zhs .
Se considera : Zu
= 8 ; Ku = 25 ; Hu = 2040 .
Vu - 75000 RON strung CNC
30000
RON masina de frezat
2800
RON strung frontal
25000
RON masina de debitat

A1 =
9,61 RON/buc
A2
= 19,33 RON/buc .
Bibliografie
- Vlase A, s.a. Regimuri de aschiere,
adaosuri de prelucrare si norme tehnice de timp, E.T.,
Bucuresti, vol. I 1983
- Vlase A, s.a. Regimuri de
aschiere, adaosuri si norme tehnice de timp, E.T.,
Bucuresti, vol. II 1987
- Vlase A, s.a. Regimuri de
aschiere, adaosuri si norme tehnice de timp, E.T.,
Bucuresti, vol. III 1987
- Vlase A, s.a. Tehnologia
constructiilor de masini, E.T., Bucuresti 1996
- Picos C. s.a. Proiectarea
tehnolgiilor de prelucrare mecanica prin aschiere, E.
Universitas, Chisinau, vol. I 1992
- Picos C, s.a. Proiectarea
tehnologiilor de prelucrare mecanica prin aschiere, E.
Universitas, Chisinau, vol. II 1992
- Blaer P., s.a. Cartea maistrului
prelucrator, E. T., Bucuresti, 1986
- €Fonte si oteluri - Standarde si comentarii in
vigoare
- €Scule aschietoare Standarde in
vigoare
- Bragaru A., s.a. SEFA DISROM
Sistem si metoda, E.T., vol. I si II, Bucuresti 1982
- Rosculet V., s.a.
Proiectarea dispozitivelor, E.D.P., Bucuresti 1982
- Tache V., s.a. Proiectarea
dispozitivelor pentru masini unelte, E.T., Bucuresti, 1995 .
- €Notite de curs